During its meeting, the FIA World Motor Sport Council has approved the sports first ever common vehicle standards for Drifting Cars, representing a milestone in the growing professionalism in the discipline.
Following a proposal from the FIA Drifting Commission, the new standards, dubbed as DC1, relate to the professional classes of the sport, and were compiled in cooperation with industry experts from the leading drift series around the world.
Until now, no common standards have existed for drift cars, with each event, series and/or ASN implementing their own regulations. These new standards will allow teams to build to a common set of regulations which can be adopted worldwide, thus making it much easier for competitors to use the same car across multiple events, enabling the sport to grow further.
According to FIA Drifting Commission President Akira Iida, the regulations are something that have been desperately needed for a long time.
“Up until now, competitors have had to pick a series and build a car for those regulations without knowing if it could be used anywhere else”, stated Iida.
“Our sport is still developing and most competitors simply don’t have the budget to build multiple different cars to run in different championships. These common standards should greatly simplify the process for both the competitors and the series that they run in and is just the first in a number of measures that the Drifting Commission plans to introduce to take the sport to expand the sport further.”
When creating these new regulations, the FIA has made a conscious effort to maintain the unique spirit of drifting.
“Drifting is unlike most other motorsports and it requires a unique approach”, said FIA Technical Director Gilles Simon.
“We have attempted to keep all the elements that make the sport exciting and engaging for drivers and fans alike, such as engine configuration and power output, which will both be left open for the competitors to determine. Instead we have contributed our expertise where it is most required, improving the safety of the cars by instilling FIA standards throughout.”
Simon concluded by reiterating that the goal of the new regulations is to raise all current Pro Class cars up to the same level.
“I believe that the majority of the top level cars that currently exist will find that they can already comply with minimal to no modifications, but these are not the cars that we are targeting. Our goal is instead to raise the standard of the other cars on the grid to ensure consistent safety levels throughout.”
As the DC1 regulations are aimed towards the Professional Classes of the sport, over the next year the Drifting Commission and FIA Technical department will continue to work together on similar regulations for both the Semi-Professional and Amateur Classes as well, completing the drifting pyramid.
The FIA Specific Regulations for DC1 Drift Vehicles are:
ELIGIBLE CARS
- Eligible Vehicles must be considered a “production Vehicle” and have had a minimum build run of 500 units. Eligible body styles include: coupe, sedan, station wagon, have no more than 5 doors.
- Vehicles must maintain the original OEM unibody/chassis and / or frame structure between the OEM front and rear suspension mounting points.
- Each Vehicle must have an FIA Technical Passport for Drifting which must be presented at scrutineering or at the request of an FIA official. (to be specified)
- Vehicles that do not meet the above eligibility criteria must be accepted by the FIA Drifting Commission and the FIA Technical Department.
AUTHORIZED MODIFICATIONS AND ADDITIONS
- These regulations are written in terms of authorization; therefore, what is not expressly authorized hereinafter is prohibited.
DIMENSIONS, POIDS, LEST / DIMENSIONS, WEIGHT, BALLAST
MINIMUM WEIGHT
- 950 kg
MAXIMUM WEIGHT
- 1500 kg
BALLAST
- Ballast permitted. Maximum allowable ballast 25 kg. Ballast must only serve the unique purpose of adding weight to the Vehicle. Ballast must only be mounted between front and rear axle. Ballast Blocks must weight no less than 5 kg each and cannot be made of liquid or any type of pellets or granulated material. Ballast must be securely fastened with a minimum of two (2) 8mm – 8.8 Grade bolts per 5 kg, attached to the Chassis. No weight shifting devices are allowed including but not limited to hydraulic, pneumatic or electronic devices.
ENGINE
ENGINE
- Only one internal-combustion automotive-type engine permitted. Engine substitutions and modifications are free, but may only run on petrol or ethanol blends. Electric and Hybrid powered systems are eligible for competition with prior written approval from the FIA Technical Department.
FLYWHEEL
- The use of cast iron flywheels is prohibited. The use of flywheels certified for Motorsport is recommended.
TURBOCHARGER
- Any kind of automotive Turbocharger permitted. Turbocharger must remain unaltered in manufacturer condition.
SUPERCHARGER / PRO-CHARGER
- Any kind of automotive Supercharger or Pro-Charger permitted. Supercharger or Pro-Charger must remain unaltered in manufacturer condition. Manufacturer Overdrive limits apply.
NITROUS OXIDE
- If the use of Nitrous Oxide is permitted, it must be commercially available. Maximum one Nitrous bottle limited to 20lbs. permitted. If installed in driver compartment, bottle must be equipped with a relief valve and vented outside of driver’s compartment. The Bottle must be stamped with a CE or DOT marking, must have a minimum 124 bar rating and must be securely mounted by a minimum of 2 screw-locked metallic straps (no hose clamps or tie wraps).
- Anti-torpedo tabs are required. The hoses from the bottle to the solenoid must be high pressure, steel braided or FIA accepted. A Hobbs switch or an equivalent system is mandatory and must be installed so that the nitrous system may only be activated when there is sufficient fuel pressure. Commercially available, thermostatically controlled, blanket-type warmer accepted. Any other external heating of the bottle is prohibited. All vehicles using a bottle of nitrous oxide must bear a sticker according to Drawing 304-3. The sticker must be clearly visible and will be located in a place which is unlikely to be damaged in the event of an accident and which is near to the competition number.
- The legal requirements of the hosting country concerning the use and handling of Nitrous Oxide must be obeyed at all times.
FUEL - FUEL SYSTEM
- Unleaded Racing fuel, max. 85% ethanol permitted. The use of Diesel, natural gas or propane is prohibited.
FUEL SYSTEM - LOCATION
- All fuel cells, lines, pumps, valves, etc. must be outside the Drivers compartment and within the confines of the Vehicles structure. Fuel-distribution blocks and fuel-pressure gauge isolators must be located at least 150mm forward of the flywheel area. Only Fuel pressure isolators, with steel braided lines, may be mounted on firewall.
FUEL CELL
- Fuel cell meeting FIA Standard FT3, FT3.5, FT5-1999 mandatory. Only one Fuel Cell permitted. Fuel cell must be vented to outside of the body. The fuel cell, the filling and ventilation systems must be separated from the cockpit by a fireproof and liquid-proof protective device. Fuel cell must have positive-lock cap. Fuel cell must be securely mounted and be at least 200mm inside of the Vehicles structure. Artificial cooling or heating systems (i.e. cool cans, ice, Freon, etc.) prohibited. Circulating systems, not part of normal fuel-pump system, prohibited. Fuel Cell must be bladder type. Pressurized refiling is prohibited.
- The ventilation line of the fuel cell as far as the valves described below must be fitted with a system complying with the following conditions:
- Gravity activated roll-over valve
- Float chamber ventilation valve
- Blow-off valve with a maximum over pressure of 200 mbar, working when the float chamber ventilation valve is closed (see also Appendix J Art. 253.14 of the International Sporting Code).
FUEL LINES
- All non-OEM fuel lines (including gauge and/or data recorder lines) must be metallic, steel or nylon braided and be fitted with AN hose ends. (see also Appendix J Art. 253.3 of the International Sporting Code)
- No Fuel line may be routed through the Drivers compartment.
FUEL PUMP
- Vehicles with a non-OEM-type mechanical fuel pump must have a quick-action fuel shutoff valve within easy reach of driver and located in the main fuel line between the fuel tank and the carburettor and/or injectors. Fuel recirculation systems not part of the normal fuel/pump system prohibited. All electric fuel pumps must only operate when the engine is running, except during the starting process.
(see also Appendix J Art. 253.3 of the International Sporting Code)
INDUCTION
- Any induction permitted. Electronic fuel injection may monitor engine functions only. Open-loop systems permitted on production Vehicles as equipped with OEM electronic fuel injection. Utilization of vehicle performance criteria, wheel speed, prop shaft speed, vehicle acceleration, etc. by fuel-injection system prohibited.
LIQUID OVERFLOW
- Catch-can mandatory for coolant overflow, 1ltr. minimum capacity required. Must be placed outside Drivers compartment.
CHASSIS / UNIBODY - CHASSIS
UNIBODY - CHASSIS MODIFICATIONS
- The original OEM floor pan, frame and or unibody – chassis must remain structural unmodified in the area between the vertical planes created by the original forward most and rearward most suspension point or sub frame mounting point in accordance with Drawing 402-1.
- The original OEM floor pan, frame and/or unibody must remain structural unmodified in the area between the horizontal planes created by the original floor pan at the lowest horizontal plane to the roof at its highest horizontal plane.
- Items in the unmodified area that are allowed to be removed can include original rear window parcel shelf, mounts for unused OEM steering columns, unused OEM windshield wiper mounts. It is permitted to replace the exterior roof panel with a composite panel. No other structural modifications to the chassis permitted except those noted in the FIA Technical Passport and approved by the FIA Technical Delegate.
BUMPER FRAME
- All Vehicles must be equipped with front and rear bumper frames unless OEM Bumper incl. OEM Bumper frame/support is used and attached at the OEM attachment points.
- Bumper frames must be constructed of min. 25mm to max. 44mm od. Steel tubing with a wall thickness of min. 1.6mm to max. 3.2mm. All bumper frame tubing must remain hollow. Bumper frames must be fastened to the Vehicle with a minimum of four (4) 10mm fasteners/bolts per side (minimum Grade 8.8) or welded to prevent the bumper frame from being dislodged from the Vehicle. Bumper frames must be rounded off or capped off to prevent becoming locked or piercing another Vehicle. Bumper frames must at minimum span the width of the front and rear frame rails. Tubing must not be exposed and must remain behind the bumper covers with maximum clearance of 50mm between the bumper cover and the bumper frame itself. Bumper must be fixed, the use of shock absorbers, dampers, springs, pivots and slip joints is not permitted unless OEM. Bumper frames must remain in the confines of the body lines and body work without additional covers or body work extensions in order to do so.
AIR JACKS / LIFTING DEVICE
- Air Jacks and/or other automated lifting devices are prohibited.
TOWING EYE
- All Vehicles must be equipped with a rear and front towing-eye which is capable of sustaining a minimum 1.5 times of the Vehicle gross weight. The towing eye must not protrude more than 75mm out of the silhouette of the bodywork if made of metal. It must be clearly visible and painted in yellow, red or orange or must be indicated on the bodywork.
FIREWALL
- A Firewall is mandatory. Firewall must be constructed of minimum 0.8mm Steel or 1.5mm Aluminium. Any holes in the firewall must be of the minimum size for the passage of controls and/or wires, and must be completely sealed to prevent the passage of fluids or flames from the engine compartment to the Drivers compartment.
FIREWALL / TRANSMISSION TUNNEL MODIFICATIONS
- Firewall and Transmission Tunnel modifications permitted as per Drawing 406-4.
- The taper length from the firewall to the end of the transmission tunnel into the beginning of the drive shaft tunnel may be no longer than 915 mm.
- All modifications to the firewall and transmission/drive shaft tunnel must be carried out using min. 0.8mm steel or 1.5mm aluminium.
BODYWORK
BODYWORK GENERAL
- Aftermarket body panels, front and / or rear fascia’s, side skirts and wings are permitted.
- All additional body panels must be securely fastened and must correspond with the OEM Body shape.
- One-piece front end (flip - front) prohibited.
BUMPER COVERS
- The bumper covers (front & rear) must cover the structure of the bumper frame. The bumper covers must be attached at a minimum of four points to the Bodywork or Chassis. The use of cable ties for attachment purpose is permitted. The Vehicle must be equipped with both (front & rear) bumpers prior to the start of the event.
DOORS
- Driver side and Passenger Side Door mandatory, may be made from composite material.
The Inside and outside door latch / lock mechanism must be operable in all circumstances and clearly visible on both, the driver and passenger side. OEM unmodified Door hinge and Door latch mandatory.
MIRRORS
- External Driver and passenger side mirror mandatory. (see Appendix J Art. 253.9 of the International Sporting Code)
WINGS
- Wings must not be wider than and must be confined within the silhouette of the Bodywork.
- Wings must be securely bolted to the Vehicle; the use of quick release pins is prohibited. Maximum size of rear wing spill plate not to exceed 300mm x 400mm. Maximum distance between the main element and the Deck lid not to exceed 400mm. The installation of the rear Wing may not obstruct the view from any angle, or the operation of any safety device, signalling light, indicator, or other equipment. Wings with standoffs must have the endplates and the wing tethered with independent cables to the Vehicle.
HOOD & TRUNK LID
- Hood and Trunk lid may be constructed from composite material. Hood must be secured by OEM hinges and two fasteners complying with Appendix J Art. 253.5 of the International Sporting Code.
- The original locking mechanisms must be rendered inoperative or removed.
TRANSMISSION
TRANSMISSION MOUNTING
- Optionally
TRANSMISSION SPECIFICATION
- All vehicles must be equipped with a functional reverse gear. Transmission and/or final drive modifications are free, but only the rear wheels may propel the vehicle. Clutch release must be manually operated initiated by the driver’s foot. Automatic transmission prohibited. Automated, timer-type, pneumatic, electric, electronic, hydraulic, etc. shifting mechanism prohibited. Each individual shift must be a function of the driver and be controlled manually. Gear shifter and/or shift linkage must be covered with a SFI Spec. 48.1 approved shift boot.
CLUTCH ASSEMBLY
- The use of multi disc clutch systems permitted. The function of the clutch must be controlled by the driver’s foot only. No automated clutch release permitted. The use of clutch systems certified for Motorsport is recommended.
BELLHOUSING
- Flywheel shield / Bellhousing meeting SFI Spec. 6.1, 6.2 or 6.3 mandatory on all entries and must be installed to manufacturer’s instructions.
DRIVE TRAIN
DRIVE TYPE
- Only the rear-wheels may propel the vehicle.
- All-wheel drive or Front-wheel drive vehicles may be converted to rear-wheel drive.
DRIVESHAFT LOOP
- Driveshaft loop mandatory. Each end of the driveshaft must have a driveshaft loop with 360˚ enclosure.
- Each Loop must be made of min. 51mm x 6.35mm steel flat strap or 1.6mm x 22mm welded steel tubing, be securely mounted to the OEM floor and located within 152mm of the front and rear universal joint in order to support the driveshaft in the event of a U-joint failure. See Drawing 702-3.
REAR AXLE DIFFERENTIAL – FINAL DRIVE
- Aftermarket Differential permitted. Differential must be securely mounted in original position.
- Gear ratio of rear axle may be altered during competition. Welding of Side Gears and Spider gears is strictly prohibited.
STEERING
BRAKES
- Four-wheel hydraulic brakes mandatory on all vehicles. Dual master cylinders pedal assemblies permitted. Driver adjustable brake bias between front and rear axle permitted. Carbon fibre, carbon ceramic, and carbon variant brakes or rotors are prohibited. Hydraulic Handbrake for rear brakes permitted. Hydraulic shut-off valves prohibited.
STEERING
- Modification of Steering components permitted. OEM Steering lock must be removed.
SUSPENSION
SUSPENSION GENERAL
- In Car, Driver adjustable suspension prohibited. No suspension changes or adjustments (including remotely) by any means are permitted between battle runs. Examples include but not limited to sway bars and electronic shock / damper adjusters.
FRONT SUSPENSION
- Modification permitted. Any modification of the suspension design type must be permitted by the FIA Technical Department and therefore be notified in the Technical Passport.
- Minimum one hydraulic shock absorber per wheel mandatory.
REAR SUSPENSION
- Original suspension design type must remain. Minimum one hydraulic shock absorber per wheel mandatory.
SAFETY CAGE
SAFETY CAGE - GENERAL
- The use of a safety cage is mandatory. The safety cage must be identifiable by means of an identification plate affixed to it by the manufacturer; this identification plate (i.e. embedded or engraved metallic plate) must be welded to the lower part of the driver side front roll bar. The identification plate must bear the name of the manufacturer, the month and year of production and an individual serial number.
SAFETY CAGE - DEFINITIONS
Safety cage:
- A Multi-tubular structure installed in the cockpit and fitted close to the body shell, the function of which is to reduce the deformation of the body shell (chassis) in case of an impact. Plating of the safety cage is prohibited.
Main roll bar:
- Transverse and near-vertical (maximum angle ± 10° to the vertical) single piece tubular hoop located across the vehicle just behind the front seats. The tube axis must be within one single plane.
Front roll bar:
- Similar to main roll bar but its shape follows the windscreen pillars and top screen edge. The lower part of the pillar must be near-vertical with a maximum angle of 10° to the vertical towards the rear. At the mounting foot, the tube must not be rearward of the foremost point of the roll bar.
Lateral roll bar:
- Near-longitudinal and near-vertical single piece tubular hoop located along the right or left side of the vehicle, the front pillar of which follows the windscreen pillar and the rear pillar of which is near- vertical (maximum angle ±10° to the vertical) and located just behind the front seats. The rear pillar must be straight in side view. The lower part of the front pillar must be near-vertical with a maximum angle of 10° to the vertical towards the rear. At the front mounting foot, the tube must not be rearward of the foremost point of the roll bar.
Removable members:
- Removable members (Bolt in tubes) if used must be installed according to Appendix J Art. 253.8.3.2.4. of the International Sporting Code.
Mounting foot plate:
- The safety cage shall attach to the chassis in eight (8) mounting points. A 2mm thick Plate minimum 120cm² in size, welded to the end of a safety cage tube to permit its mounting to the body shell or chassis, usually onto a reinforcement plate. This plate may be welded or bolted to the body shell / chassis. When the safety cage or parts of it is bolted to the chassis, Appendix J Art. 253.8.3.2.6. of the International Sporting Code must be followed.
Reinforcement plate:
- Metal plate fixed to the body shell/chassis under a roll bar mounting foot.
Gussets:
- Gussets of such as dimple die plates are allowed along A-pillar, B-pillar, and roof structure. Dimple plate gussets must be made from steel plate no thicker than 3mm. No gussets or attachment of any form may pass from the door bars to the chassis, unibody or rocker panel. See Appendix J Art. 253.8.2.14. of the International Sporting Code for additional information.
SAFETY CAGE - SPECIFICATIONS
- Basic structure: The base structure must be constructed according to one of the following designs:
- Base structure 1: 1 main roll bar-1 front roll bar-2 longitudinal members-2 backstays-6 mounting feet
- Base structure 2: 2 lateral roll bars-2 transverse members-2 backstays-6 mounting feet
- Base structure 3: 1 main roll bar-2 lateral half-roll bar-1 transverse member-2 backstays-6 mounting feet
- The near-vertical part of the main roll bar (or the rear pillar of the lateral roll bar) must be as close as possible to the inner side panels of the body shell and must have no more than one bend. The pillar of the front roll bar (or the front pillar of a lateral roll bar or half-roll bar) must follow the windscreen pillar as closely as possible and must have no additional bends below that where it ceases to follow the windscreen pillar. The following connections must be situated at the roof level:
- Longitudinal members to the front and main roll bars
- Transverse members to the lateral roll bars
- Semi-lateral roll bar to the main roll bar
- The backstays must be attached at the roof level and near the top outer bends of the main roll bar, on both sides of the car. They must form an angle of at least 30° with the vertical, must run rearwards and be straight and as close as possible to the inner side panels of the body shell.
COMPULSORY MEMBERS AND REINFORCEMENTS
- Diagonal members: The safety cage must have two diagonal members on the main roll bar according to the Drawing 102-7. Members must be straight and may be removable. The lower end of the diagonal must join the main roll bar no further than 100 mm from the mounting foot. The upper end of the diagonal must join the main roll bar no further than 100 mm from its junction with the backstay.
- Roof reinforcement: The upper part of the safety cage must be reinforced with members according to one of the Drawings 102-9, 102-10 or 102-11.
- The members may follow the curve of the roof. For competitions without co-drivers, in the case of Drawing 102-10, only one diagonal member may be fitted but its front connection must be on the driver’s side.
- The ends of the members must be less than 100 mm from the junction between roll bars and members of the base structure (not applicable to the top of the V formed by reinforcements in Drawings 102-10 and 102-11).
- Under no circumstances may any of the Door bar Side protection penetrate the “A” or “B” pillar of the chassis.
- The connection of the door bars to the windscreen pillar reinforcement (if used) is permitted.
- If the two door bars do not intersect as they do when forming an “X” shown in Drawing 103-2, then a minimum of two vertical tube sections shall connect the upper and lower door bars as shown in Drawing 103-3. “NASCAR-Style” Side protection bars, which extend into the outer door skin as shown in Drawing 103-4 are permitted. If the “NASCAR-Style” configuration is used, the outer bars must have a minimum of three vertical tube sections connecting the upper and lower door bars. In the case of Drawing 103-4, it is not mandatory that the upper and the lower longitudinal members are parallel.
- In the case of Drawing 103-2, 103-3 and 103-4, it is required that the attachment points of the longitudinal members are directly connected to the front and the main roll bar uprights.
- In the case of Drawing 103-3, the door bars may also run parallel.
- If these upper attachment points are located in front of or behind the door opening, this height limitation applies to the corresponding intersection of the member and the door opening (side view). In the case of Drawing 103-2, it is required that at least one part of the "X" is a single Tube.
- The Side protection must be as high as possible, but its upper attachment point must not be higher than half the height of the door opening measured from its base.
- They Tubes may be removable in lieu with Appendix J Art. 253.8.3.2.4. of the International Sporting Code.
- One longitudinal member may be added to each of the designs shown in the Drawings below. The design must be identical on both sides.
- Door bars Side protection: Longitudinal members (Door bars) must be fitted on each side of the vehicle according to Drawings 103-2, 103-3 or 103-4. Drawings may be combined.
- Windscreen pillar reinforcement: A Windscreen pillar reinforcement is required in all safety cages on each side of the front roll bar if dimension "A" in Drawing 104-2 is greater than 200 mm. It may be bent on the condition that it is straight in side view and that the angle of the bend does not exceed 20°.
- Its upper end must be less than 100 mm from the junction between the front (lateral) roll bar and the longitudinal (transverse) member. Its lower end must be less than 100 mm above the (front) mounting foot of the front (lateral) roll bar.
- Anti-intrusion Bars: The anti-intrusion bars are intended for additional foot protection.
- All vehicles must be equipped with anti-intrusion bars which must connect in two places at the lower part of the front roll bar and the firewall but not penetrating any panel. See Drawing 105-2.
ADDITIONAL MEMBERS AND REINFORCEMENTS
- Any number of additional reinforcing tubes, gussets or supports within the confines of the safety cage permitted.
- Additional reinforcements must comply with Appendix J Art. 253.8. of the International Sporting Code.
SAFETY CAGE TUBE SPECIFICATIONS
NOTE:
- For unalloyed steel, the maximum content of additives is 1.7 % for manganese and 0.6 % for other elements. In selecting the steel, attention must be paid to obtaining good elongation properties and adequate weld ability. The tubing must be bent by a cold working process and the centreline bend radius must be at least 3 times the tube diameter. If the tubing is ovalised during bending, the ratio of minor to major diameter must be 0.9 or greater. The surface at the level of the bends must be smooth and even, without ripples or cracks.
- Guidance on welding: Welding must be carried out along the whole perimeter of the tube on all connections (except where bolt in is permitted). All welds must be with full penetration using the gas-shielded Tungsten Inert Gas welding process. The grinding of welds is prohibited. When using heat-treated steel the special instructions of the manufacturers must be followed.
SAFETY CAGE PADDING
- The driver side of all tubes of the cage identified on Drawing 108-3 in red and all roof reinforcements must be fitted with padding in compliance with FIA standard 8857-2001 type A (see Technical List n°23).
- Each padding must be fixed in such a way that it is not moveable from the tube.
TIRES AND WHEELS
TIRES
- Tires must be of automotive type with DOT or EU rating. The use of tire warmers, chemical treatments, or any means to artificially enhance tire performance is prohibited including grooving or shaving.
WHEELS
- Must be automotive-type wheels suitable for street use. Minimum wheel size: 15 inches (unless originally equipped with smaller wheels and Vehicle is equipped with original engine). The thread engagement on all wheel studs to the lug nut, or lug bolt to wheel hubs, must be equivalent to or greater than the diameter of the stud. Length of the stud/bolt does not determine permissibility; length of the engagement between the stud and lug determines permissibility. Automotive-type wire, centre lock or mono lock wheels prohibited. Bead locks, wheel screws and any means of any kind of attachment between wheel and tire is prohibited. Use of Wheel Spacers permitted, only one spacer per wheel.
- Spacers with a thickness greater than 20mm must be equipped with their own mounting bolts to the hub. The maximum permitted spacer thickness is 60mm per wheel.
INTERIOR
SEATS, ANCHORAGE POINTS AND SUPPORTS
- Driver Seat must comply with FIA Standard 8855-1999 or 8862-2009.
- See Appendix J Art. 253.16 of the International Sporting Code for fitting and mounting instructions. No passengers permitted during competition.
DRIVERS COMPARTMENT
- The Drivers Compartment must be designed in such a way as to allow the driver wearing his complete driving equipment, being seated in a normal driving position with the seat belts fastened and the steering wheel in place to escape out of the Vehicle in maximum 8 seconds through the Driver Side Door, or in maximum 14 seconds through the Passenger Side Door.
- No pressurised containers (except Fire Extinguisher system or fresh air supply) permitted in the Drivers Compartment.
SHEET METAL
- Driver compartment interior must be aluminium, steel or ASN-accepted composite material. Magnesium prohibited.
BODY
WINDSHIELD
- Mandatory, must be in good condition and free from cracks. May be replaced with shatterproof material, 4.5mm minimum thickness securely bolted in place. Windshield may not be cut for scoops, carb, etc.
- Windshield tint is prohibited.
WINDOWS
- Door, quarter and rear window must be OEM glass or shatterproof material with minimum thickness of 3mm and securely bolted in place. Front driver and passenger side windows not mandatory. Side windows and rear windows must be clear, use of tint or wrap is prohibited.
ELECTRICAL
BATTERIES
- Batteries (max. two) may not be located in driver compartment. Each Battery must be securely fastened to the frame or unibody with a minimum of two 8mm bolts.
CIRCUIT BREAKER
- Mandatory on all Vehicles. The general circuit breaker must cut all electrical circuits (battery, alternator or dynamo, lights, ignition, electrical controls, etc.) and must also stop the engine. It must be a spark-proof model, and must be accessible from inside (in Drivers reach) and outside the Vehicle. As for the outside, the triggering system of the circuit breaker must compulsorily be situated at the lower part of the windscreen mountings on the driver side A-pillar. It must be marked by a red spark in a white-edged blue triangle with a base of at least 120mm. See Drawing 141-3.
LIGHTS
- All OEM lights must remain in place, Headlights, tail lights and brake lights must function normally.
- Brake lights and tail lights may only be red, tinting is prohibited. Rearward facing strobe lights of any colour is strictly prohibited. Any variation of red and or orange coloured headlights is prohibited.
SUPPORT GROUP
COMPUTER
- The choice of the engine Electronic control unit (ECU), engine control software, sensors and engine loom is free.
- During FIA competition, a portable computer (e.g. laptop, PDA, Palm Pilot, programmer, etc.) must be securely mounted when competing. All functions or values must be pre-set prior to this point.
- Any use of Electronic Stability Program - Anti-Lock Brake System - Anti Slip Regulation or any other electronic, pneumatic or manual Driver assisting system is strictly prohibited. The use of Wheel and / or Driveshaft Speed Sensors is prohibited and those must be removed. Any device (mechanical, hydraulic, pneumatic, electrical, optical, etc.) other than OEM type or supplied by the organizer, which assists in determining track location of the competitors own or opponent’s Vehicle is prohibited.
- Discovery of a device which displays, indicates, or transmits “on track” or “track location” type data other than installed by the Organizer, will be grounds for immediate exclusion from the event. Additional penalties may be imposed in accordance with the FIA International Sporting Code.
SAFETY
FIRE EXTINGUISHER SYSTEM
- All vehicles must be equipped with a fire extinguishing system meeting FIA Standard “FIA Standard for Plumbed-in Fire Extinguisher Systems in Competition Cars”, (Technical List N°16) or FIA Standard 8865-2015 (Technical List N°52). The minimum quantity of extinguishant for systems of Technical List n°16 is 4 kg. The system must be approved in order to release the extinguishment into the cockpit and the engine compartment by the means of nozzled outlets. The system installation must comply with Article 253.7.2 of Appendix J to the International Sporting Code, following the manufacturer’s specifications, inside the Drivers compartment, and must be visible from the outside of the Vehicle. Safety pins (if equipped) must be red-flagged and be removed before entering the designated burn out area.
WINDOW NET
- A window net designed according to Article 253.11.2 of Appendix J to the International Sporting Code is mandatory on the Driver side window. Arm restraints complying with SFI Spec. 3.3 can be used in lieu of a Window Net.
DRIVER RESTRAINT SYSTEM
- Minimum 5-point Driver restraint system meeting FIA Standard 8853/98, 8853-2016 mandatory. (see also Appendix J Art. 253.6 of the International Sporting Code)
ARM RESTRAINTS
- Permitted if Window Net is used, otherwise mandatory.
HEAD AND NECK RESTRAINT DEVICE / FHR
- The use of a head and neck restraint system is mandatory.
- The device or system must meet FIA Standard 8858-2002 or 8858-2010 and must display a valid label accordingly.
PROTECTIVE CLOTHING
- The use of synthetic, non-flameproof materials in contact with the driver’s skin is not permitted.
- A Driver Suit including long underwear, Gloves, Footwear and Balaclava meeting FIA Standard 8856-2000 or 8856-2018 mandatory. Chapter III – Drivers’ Equipment, Article 2 “Flame-resistant clothing”, Appendix L to the FIA ISC must be respected.
HELMET
- A full-face helmet and visor meeting FIA Standards 8858-2002, 8858-2010, 8859-2015, 8860-2004, 8860-2010, 8860-2018, mandatory. The helmet visor must be closed at all time during on-track activities.
- No modifications or attachments such as cameras, etc. are permitted unless approved in the original homologation. It is recommended that drivers use a balaclava homologated to FIA 8856-2000 or FIA 8856-2018 standard, and that is indicated in the technical lists as a balaclava that reduces the loads transmitted to the driver’s neck while the helmet is being removed.
For more information, visit www.fia.com.
Related Articles

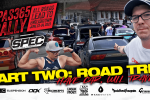
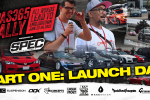
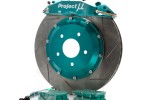
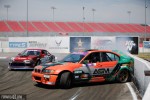
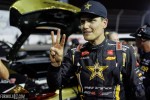